CNC Controls & Software: Intuitive, Powerful, Dependable
FlashCut’s Windows CNC Controls and Software Architecture
Microstepping
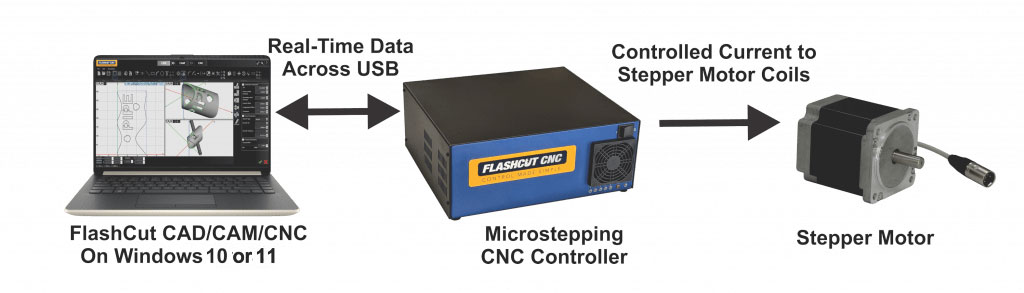
Servo
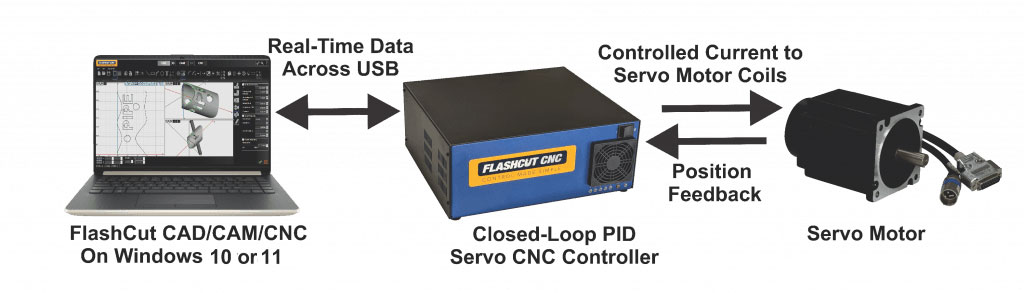
FlashCut CNC controller kits are composed of the following parts:
FLASHCUT CAD/CAM/CNC SOFTWARE
The FlashCut Software running under Windows is the CAD/CAM interface and CNC operator control panel. It processes all of the real time graphics and user interface commands. It sends motion commands to the CNC Controller over a high speed USB connection. Since Windows is NOT a real time operating system, FlashCut sends all of the motion commands to the CNC Controller over a Hi-Speed USB link to reliably process all of the real time motion.
SERVO OR MICROSTEPING CNC CONTROLLER
Our Microstepping Controllers and Digital Servo Controllers all have a USB Signal Generator along with an integrated power supply and drives to power the motors. The Signal Generator uses three dedicated microprocessors doing parallel processing to generate precision-timed, uninterrupted motion signals to drive up to five stepper or digital servo drives with full multi-axis interpolation using “Continuous Contouring”.
The stepper systems are all precision microstepping and our digital servos use PID position feedback from optical encoders to maintain a true position.
MOTORS
The motors provide the physical torque at a given speed to move the axes on the machine precisely as commanded by the FlashCut CNC Controller.
STEPPER VS SERVO
Stepper control is the most cost-effective way to control a machine tool. The accuracy is exceptional, and the price is very reasonable. All of our stepper systems are micro-stepping, giving you great smoothness and accuracy. The only limitation is that the maximum speeds for rapid moves and cutting moves are not as high as for servo control.
Servo control uses feedback from an encoder to constantly monitor the machine tool’s exact position. Using the feedback signals, the control system can achieve very high speeds and perfect accuracy, even under very strenuous conditions.